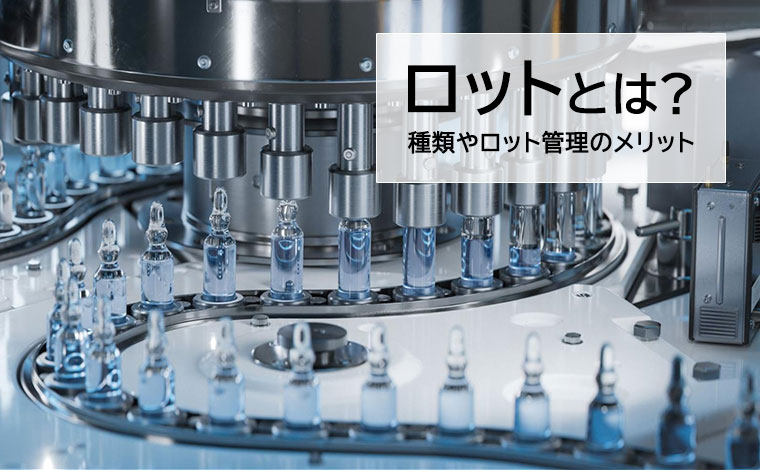
ロット(lot)とは、同じ製品をまとめて管理する際の最小単位のことです。
ある程度の数量をまとめてロットで管理することで、1つひとつの製品を別々に管理する場合と比較して、在庫管理の効率化を図ることができます。日々の煩雑な在庫管理を改善したいと考えている担当者も少なくありません。
ロットは業界問わず幅広く使われている言葉ですが、本記事ではEC通販における物流倉庫のロット管理にフォーカスして解説します。ロットの種類や生産管理におけるメリット、注意点について理解し、在庫管理の効率化を目指しましょう。
目次
1ロットとは
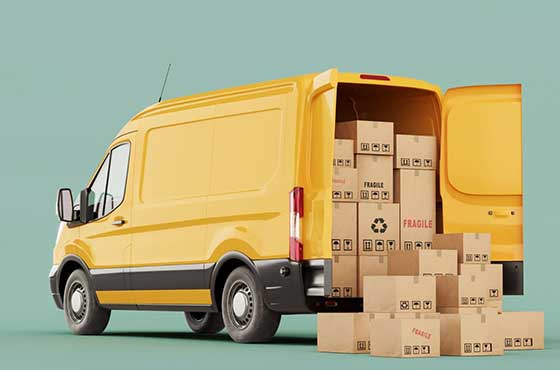
「ロット(lot)」とは、一定の数量をまとまりとした最小単位のことで、物流業界では「同じ時期に作られた同一製品をまとめて管理する際の最小単位」を意味し、製品を製造する際は、ロットごとに番号を振って管理するのが一般的です。
「ロット管理」とは、このロットを製造から出荷まで一貫して管理することであり、製造現場だけではなく、通販での保管・出荷においても重要となります。
ロット管理を行うことで、製造年月日や製造ラインが同じ製品ごとに管理が可能になります。これにより、販売効率の向上・在庫管理の効率化・トラブル時のコスト削減につながります。
また、生産頻度・生産量が多い製品の場合は、在庫管理が煩雑になりやすい課題がありますが、ロット管理を行うことで在庫状況を把握しやすくなります。
ロットの数量は企業の裁量で設定する
「1ロットは何個」という数量の規定はありません。
適切なロットの数量は製品の性質や価格によって異なるため、ロットの数量は企業の裁量で自由に決めることができます。
企業によって、ロットではなくダースで製品数量を管理するケースもあります。
ダースの場合は「1ダースが12個」と数量が決まっているため、製品ごとにロットを決める手間が省けます。
ダース管理と比較して、ロット管理は各製品ごとにロット数量を定める手間や、製品ごとに異なるロットを整理して社内共有する手間などが発生します。しかし、ロットは製品ごとに細かく最適な最小数量を決められる点や、原材料などの変化に合わせて臨機応変に数量を変えられる点がメリットです。
2ロットの種類
輸送・配送・保管の各工程において、管理しやすい数量は異なります。
そのため、物流業界では次の3つのそれぞれの行程でロットを管理します。
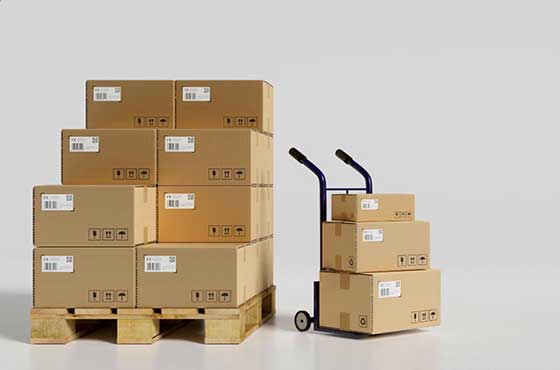
- 輸送ロット
- 配送ロット
- 保管ロット
輸送ロット
輸送ロットとは、輸送効率を高めるために、輸送物をある数量ごとのロットにまとめることです。あらかじめ輸送時の最小数量をロットとして定めておくことで、
「1ロット以下の少量貨物をトラックで輸送して1製品あたりの輸送コストが跳ね上がった」
という事態を避けることができます。
輸送ロットは貨物量によって小ロット・中ロット・大ロットに分類することもあります。
貨物量の規模は以下のとおりです。
ロットの分類 | 貨物量の規模 |
---|---|
小ロット | 1トン未満の貨物量 |
中ロット | およそ1トン以上でトラック1台分に満たない貨物量 |
大ロット | トラック1台が満車になるくらいの貨物量 |
配送ロット
配送ロットとは、配送の効率を上げるために配送物をある数量ごとのロットにまとめることです。ロット単位で注文を受け、配送時もロット単位で配送することで、在庫管理がしやすく、1点あたりの配送コストを下げることもできます。
保管ロット
保管ロットとは、製品を保管する際に、ある程度まとまった数量で保管することです。
通常は1製品ごとにバーコードを発行しますが、小さい製品の場合はバーコードを付けることが難しく、まとまった数量で1つの製品として保管するほうが管理しやすくなります。
一般的に、ロット単位で在庫管理する場合は、製品にロット番号をひもづけたまま管理します。これによって、例えばロット番号のうち、前4桁が製造年、次の2桁が製造月、その次の2桁が製造日とすると、ロット番号を見るだけで製造年月日が分かります。
3ロット管理のメリット
倉庫管理や販売の工程において、ロットごとに製品を管理するメリットは下記の3つです。
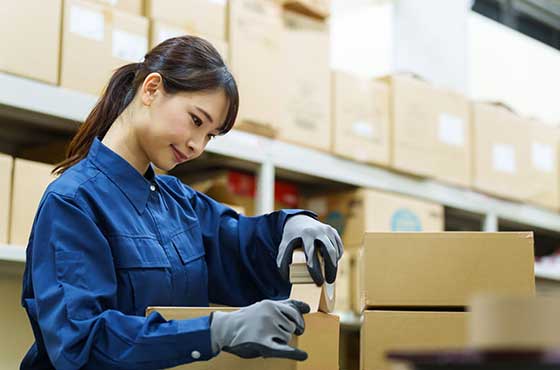
- 余剰在庫を防止できる
- 在庫管理の品質を向上できる
- 不良品を特定しやすい
余剰在庫を防止できる
最小の生産数量としてロットを定めていない場合、需要に対して過剰に生産してしまうリスクがあります。過剰に作られた製品は、販売されるまで売れ残りの在庫(余剰在庫)として保管され、保管スペースの圧迫や保管コストの増大といった問題に繋がります。そのため、最小の生産数量としてロットを定め、過剰生産・余剰在庫を防止することが大切です。
なお、一度定めたロットで生産する中で、想定していたより販売数が多く、在庫数が足りないという状況になる場合もあります。その場合は、1ロットあたりの生産数量を増やすことで、製品の在庫を増やす調整が可能です。
在庫管理の品質を向上できる
製品にロット番号をひもづけて管理することで、在庫管理がしやすくなります。
同じロット内の製品は、全て同じ時期・同じ工程で製造された製品ですので、ロット管理をすることで製造時期についても管理することが可能です。製造日が古いロットの製品から順に出荷することで、先入れ先出しを効率的に行うことができます。
不良品を特定しやすい
日頃からロット管理を行っておくと、消費者から「製品に不良品があった」との連絡を受けた際にも役立ちます。消費者から不良品のロット番号を聞くことができると、どのロットが不良の発生した製品であるかを特定することができます。
製造過程で何らかの問題が発生して不良品となっている場合は、同じロット内で製造された製品にも不良品が混ざっている可能性があります。
企業としては、消費者に不利益を与えないように、不良品の可能性がある製品を回収する必要がありますが、ロット管理をしていることにより不良品の可能性がある範囲を限定できると、一部の製品回収のみで事態を収束させることができます。
一方、ロット管理をしていない場合は、製造時期・製造工程で影響範囲を特定することが難しく、最悪の場合、世に出回る全ての製品を回収・リコールしなければならないことがあります。販売後の管理についても考えると、ロット管理によって製品の生産・保管・販売の情報を管理しておくことは非常に重要です。
4ロット管理の注意点
在庫管理の効率化などメリットが多いロット管理ですが、下記の点には注意が必要です。
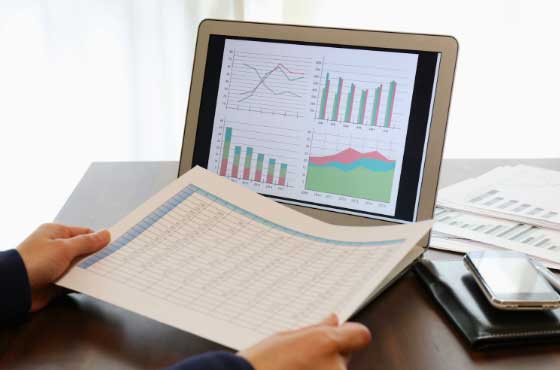
- 発注数量を間違えやすい
- 管理項目が増える
- ロット管理に非対応の倉庫がある
発注数量を間違えやすい
ある製品を100個発注するように担当者が指示を受けた際、ロットが設定されていない場合は当然ながら発注数量を100として問題ありません。
一方で「1ロット=50」と数量を定めてロット管理をしている物流現場の場合、
「発注数量を100」とすると「1ロット(50) ×100=5,000個の発注」と誤認される可能性があります。ロット管理をしている場合は発注数量を間違えやすいため、入力ミスを防ぐ対策が必要です。
また、複数の製品を取り扱う企業では、製品ごとに個別にロットを定めているケースがほとんどです。1ロットあたりの数量は製品ごとに異なるため、発注数量を間違えないように注意する必要があります。
管理項目が増える
ロット管理を行うと、在庫管理の項目が増えるため、物流現場では具体的に下記の作業が必要になります。
<物流現場で必要な作業>
- ロットごとに製品の保管場所を分ける
- 保管ケースには必ず同じロットの製品を保管し、ロット番号が分かるシールを貼る
またデータ管理の場面では、追加で下記の作業が必要になります。
<データ管理で必要な作業>
- ロット番号を管理システムに入力する
- ロットが分かれることで管理シートの行が増える
- 1ロットあたりの数量を変更する場合は、データ上でも最新のロットに変更する
このように、物流現場においてもデータ管理の場面においても、ロット管理を行うことで管理項目は増えることになります。しかし、前述したとおり、ロット管理によって製品の状態を可視化することは、余剰在庫の防止や在庫管理の品質向上につながるメリットがあります。
管理項目が増えることは、必要なコストと考えましょう。
ロット管理に非対応の倉庫がある
物流倉庫によっては、ロット管理に対応していない場合があります。
物流倉庫をアウトソーシングして利用している企業や、将来的に倉庫のアウトソーシングを検討している企業は、物流倉庫側がロット管理に対応しているかどうかの確認が必要です。
5まとめ:在庫管理の品質を向上できるロット管理
製品のロットを適切に設定することで、余剰在庫をかかえるリスクを軽減させ、在庫管理の効率化や品質の向上が可能です。また、ロット管理によって不良品が特定・追跡しやすくなることで、不良品を発見した際には早期に適切な対応ができるため、企業への信頼も高まります。
当社スクロール360では、長年培った知見とノウハウを活かし、ロット管理まで可能な物流代行サービスを提供しています。お困りのことがありましたらぜひご相談ください。
サービスはこちら